Space
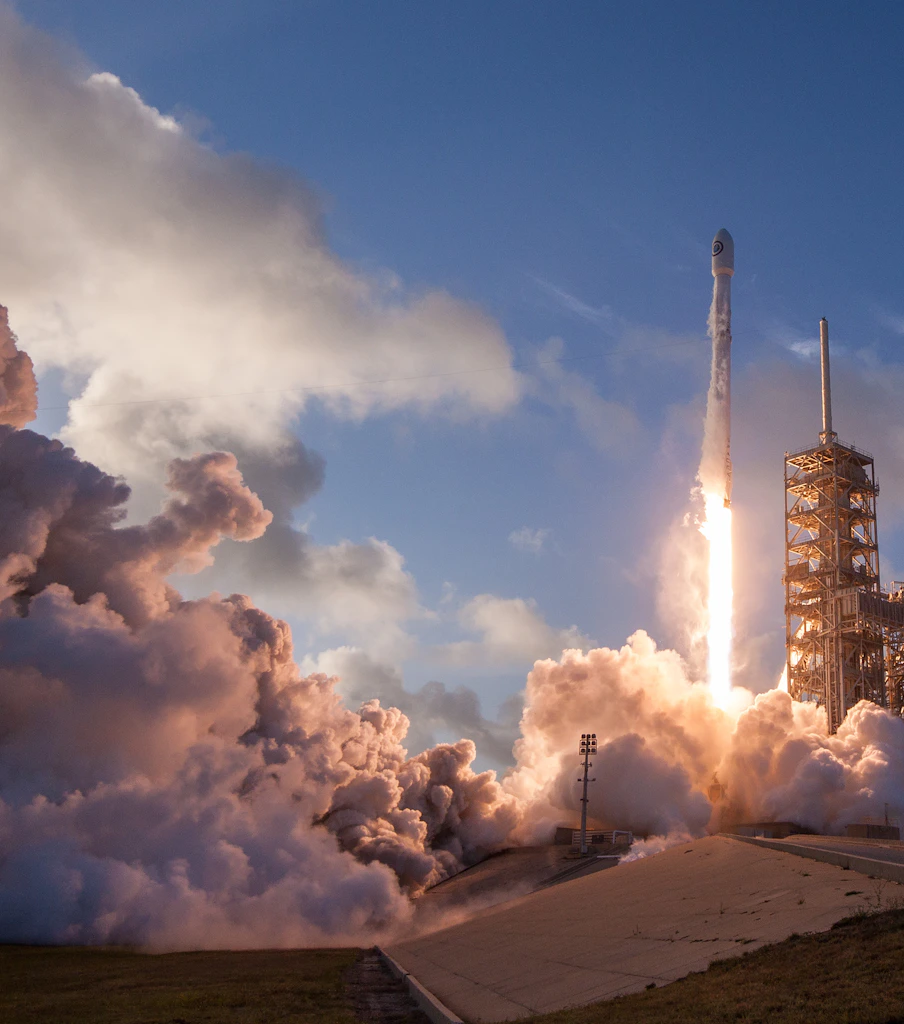
Rapidly reusable space vehicles and operation terminals
Reliable, Operable, and Profitable
Rapidly Reusable Space Vehicle System
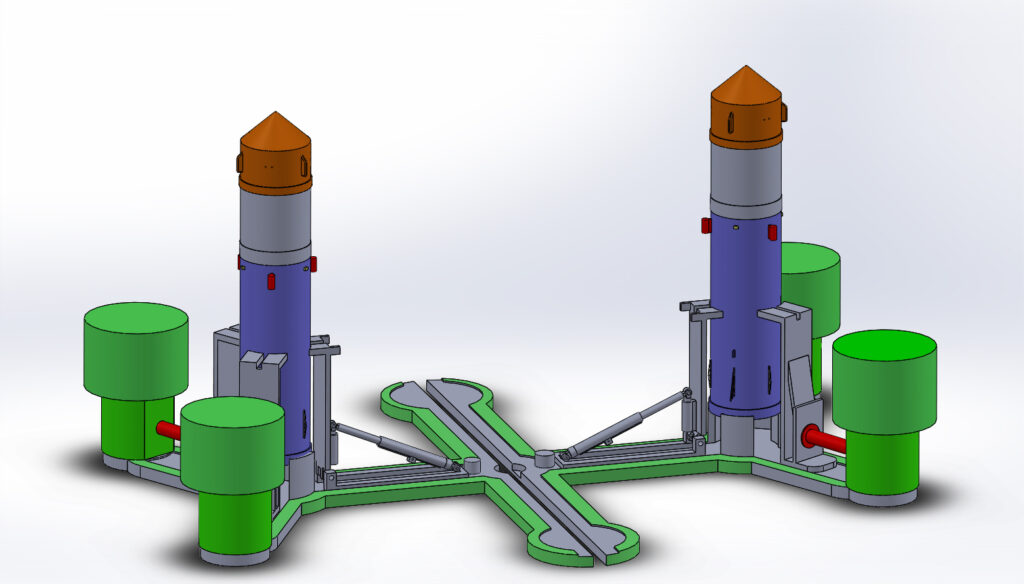
a rapidly reusable space vehicle system with a space vehicle and a hybrid operation terminal. The space vehicle is modularized functionally and structurally, and constructed with launch vehicles and a spacecraft with an inherent single fault tolerance design, an AI dual-level control model ( high and low-level liquid similar to the human brain ) rocket engine feeding subsystem to reduce fluid-related exploration by 65%, and cost and time, and It has three survivable feathers: tenacious heat shields tiles, spider landing legs, and active landing fins to secure the safe landings every time, the hybrid operation terminal is modularly constructed with vehicle carriers, and have launching and landing functions, and a renewable energy subsystem to harvest the launching thrust energy about 30% and grouping launch capability to increase efficiency and reduce the cost of launch and time
Space Vehicle Survivable Features
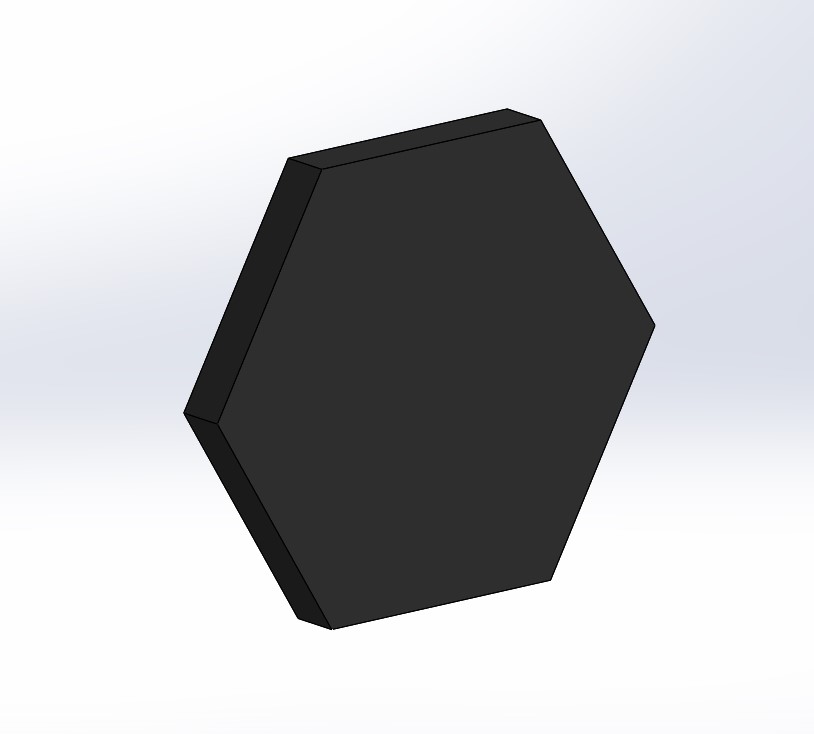
Tenacious Heat Shield Title
- Case study: On February 1, 2003, the Space Shuttle Columbia was destroyed on reentry due to a failure of the TPS. The investigation team found and reported that the probable cause of the accident was that during launch, a piece of foam debris punctured an RCC panel on the left wing’s leading edge and allowed hot gases from the reentry to enter the wing and disintegrate the wing from within, leading to eventual loss of control and breakup of the shuttle. On Dec. 11, 2022, Artemis 1 returned to the Earth, the landmark 2022 moon mission was successful, but questions remain about how Orion’s heat shield performed.
- Solutions: our studies show that the two main issues for the heat shield tiles failure are (1) thermal change between different materials and (2) joint methods, we developed the structures to minimize the thermal changes between different materials, revolutionize the joint methods, even with thermal changes, the tenacious heat shield tiles remain intact with multiple reentries, no company or organization got that far to solve this problem since the space shuttles were introduced in 1981, no need repair for each landing, this issue is a life and dead issue for rapidly reusable space vehicle growing.
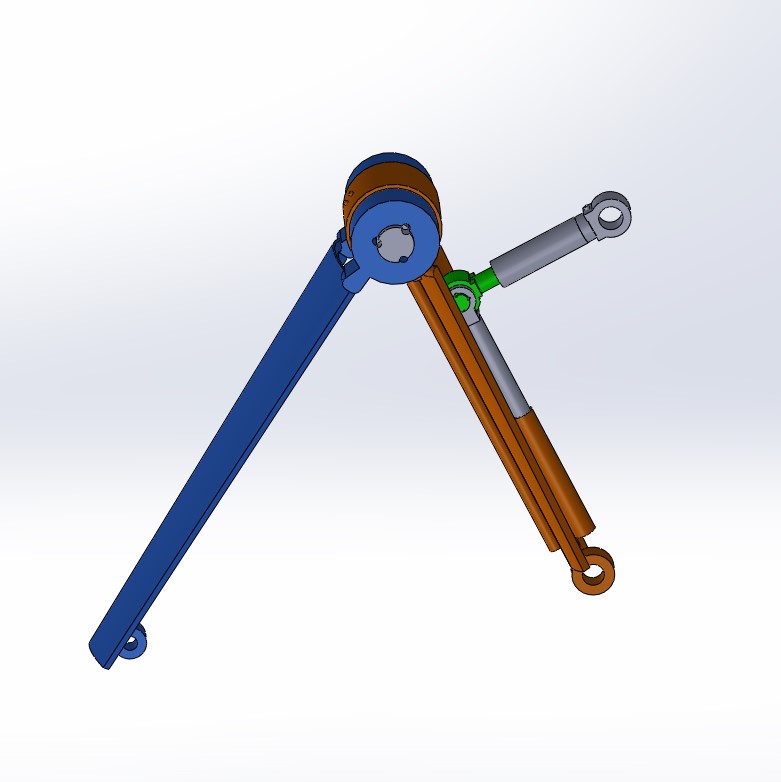
Spider Landing Leg
- Case Study: On August 28, 2024, SpaceX’s Falcon 9 rocket was grounded by the Federal Aviation Administration, following the failed landing of a first-stage booster, serial number B1062. On December 27, 2023, a Historic SpaceX Falcon 9 booster number B1058, topples over and is lost at sea. On November 20, 2020, the Falcon 9 booster that launched four astronauts toward orbit arrived on a SpaceX drone ship with a lean.
- Solutions: High school math teaches us that a plane is fully defined by three points when we walk into a restaurant, if we find a four-legged table, most likely we will check if the table is stable, why because a plane with four points is over defined. so the table is unstable, even though it looks stable, we studied the legs of many animals and insects and found a spider with a simple leg structure to sustain high impact, even though the spider has eight legs, as we remove one of the legs at a time, the spider adjusts the balance right away, we discovered a secret balance mechanism of spider, so we developed spider landing legs to overcome the current problems, with AI High-level and low-level control model and the spider leg structure, three main legs are designed with spider structure and controlled by AI high-level control and three standby legs are designed with spider structure and controlled with AI low-level model like the spider balance mechanism in case the main legs fail, remember anyone asks you why, you know the answer.
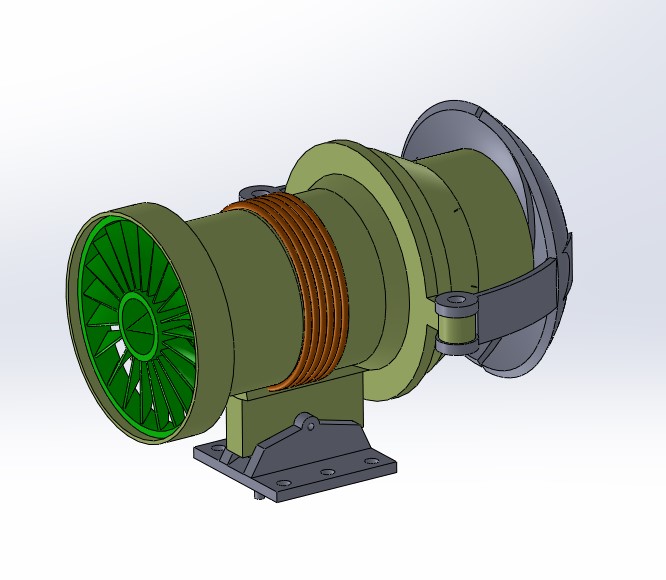
Active Landing Fin
- Case Study: On August 28, 2024, SpaceX’s Falcon 9 rocket was grounded by the Federal Aviation Administration, following the failed landing of a first-stage booster, serial number B1062. On December 27, 2023, a Historic SpaceX Falcon 9 booster number B1058, topples over and is lost at sea. On November 20, 2020, the Falcon 9 booster that launched four astronauts toward orbit arrived on a SpaceX drone ship with a lean.
- Solutions: Our study shows the landing burn for providing a safe landing is a very problematic solution, because of the nature of vertical landing without a stable plane but the unstable landing burn before landing, unlike static cranes, they are static with ground friction and support and additional weight to counterbalance any side load in the normal weather on the Florida coast, second the timing of landing turn is critical for a safe landing, so we developed the landing active Fins located at proper locations to replace the landing burn, so any uncertainty of landing is eliminated, with spider landing legs, so the reliable, operable and profitable space travel becomes a reality as we use airplanes to travel every day unless there is severe weather.
AI Pogo-free Liquid Rocket Engine Feed System
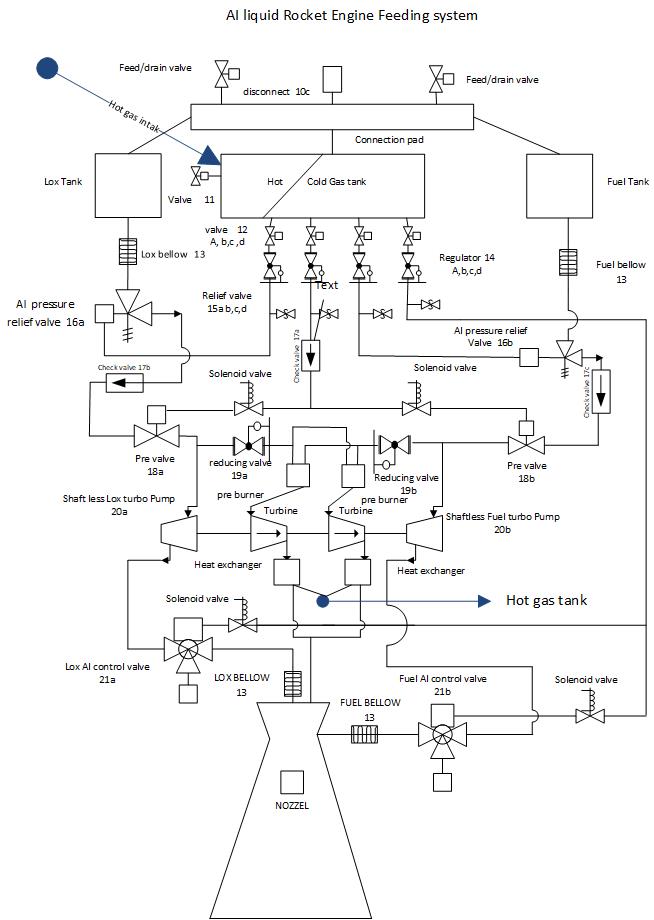
- Case Study: Current Liquid Rocket Engine Feed Systems have many problems. a few small manufacturers provide most parts of all feed systems without strong engineering support for the feed systems and rely on rocket manufacturers’ expertise. but the rocket manufacturers are not component specialists, and even if they make their parts, they are still not up to the tests, the following are the main issues (1) Specifications are mixed with NASA ( or standards or NASA approval standards), and modified standards from other standards, the mixed specifications not only complicate the system design but also increase interconnection cost and time (2) Designs, each component is designed based on the component level performance, not a system level performance, those designs very often causes chatter and joint leaks, vibrations, pogo and reduce the system level reliability, so those design have no inherent single fault tolerance, many of them are mechanically assembled, but their functions are wrong , in case of point, two pressure relief valves are arranged in series (3) manufacturing process , there are no comm manufacturing standards to secure a good quality of the feed system, each component manufacture has own process , method and practice , but the condition of the manufacturing not only cause different quality of parts but cause logistic nightmare.
- Solutions: The AI Liquid Rocket Engine Feed System is a game-changer with High and low-level controls similar to our humans, we never think about how fast to digest foods, how fast the heartbeat should be, or how fast we have to breathe, our brain will tell our body without our thinking, but we have to think about selecting foods we eat, and go to see doctors if our hearts have problems, why it that, because our brain has two functions: a low-level control and high-level control, our feeding system has the similar functions, a low-level control with self fast -acting and self -feedback, a high-level control with sensors, chips, and input, second they have an inherent single fault tolerance design based on NASA standards either in a part level or a product level or a system level (3) each part or component is subject to NASA or relevant design and test standards, not modified for the other no NASA or irrelevant standards.
AI Chatterless Tank Pressure Relief Valve
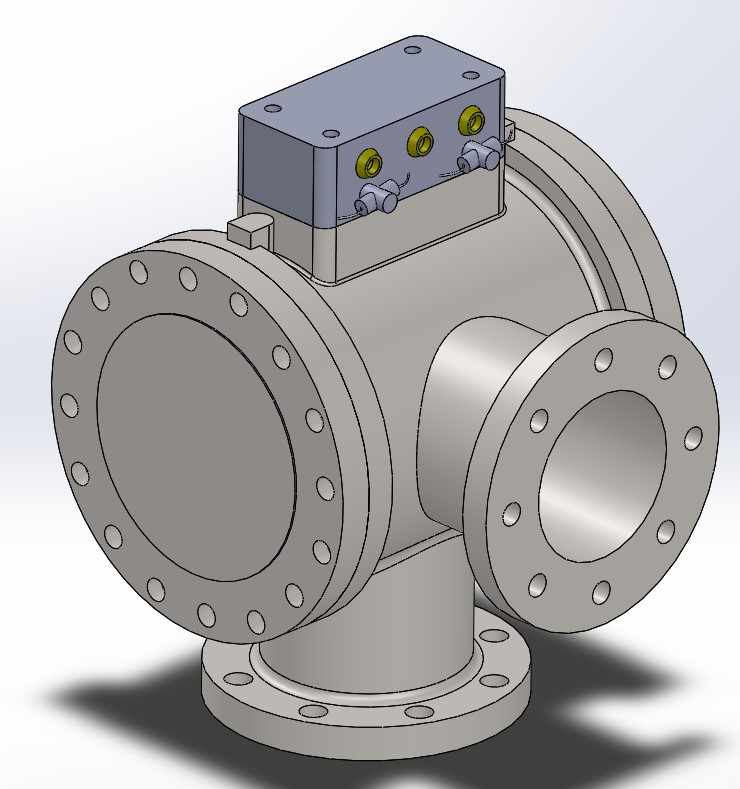
- Case study: (a) Astrobotic Technologies launched its spacecraft atop a new rocket for the first moon mission from Cape Canaveral, Florida, at 2:18 a.m. ET on Jan. 8, 2024, in an attempt to be the first company to touch down on the moon. Its lander, named Peregrine after the world’s fastest bird, was packed with five NASA payloads among other nations’ and commercial customers’ cargo, but failed duet fuel tank relief valve leaked (b) May 6, 2024, The Starliner’s crew, commander Barry “Butch” Wilmore and co-pilot Sunita Williams came within about two hours of launch, only to be derailed by trouble with a pressure relief valve in their Atlas 5 rocket.
- Solutions: we developed a compact pressure relief valve and a control box on the top, the valve has two independent plugs, two independent action chambers to provide pressure sensing, relief action, and reseating, and abroad red crew actions, two independent seats, the plug is designed with two critical features: a position seal to prevent FOD with triple seals, a moving stabilizer to prevent the plug from jamming without causing vibrations, the control box is provided with two redundant solenoid valves, AI high level mode and low-level control mode , the High-level control include (1) ground pressure test, on abroad red team override to prevent leaks and vent LOX before landing, the low-level control includes pressure relief over a set pressure, switch between the high-level control mode and low-level control mode, the valve size is from 3″ to 12″, they are direct acting, light weights with various materials selections, pressure up to 22 bar, the medium includes lox oxygen, liquid fuels.
AI Leakless Feed/drain valve
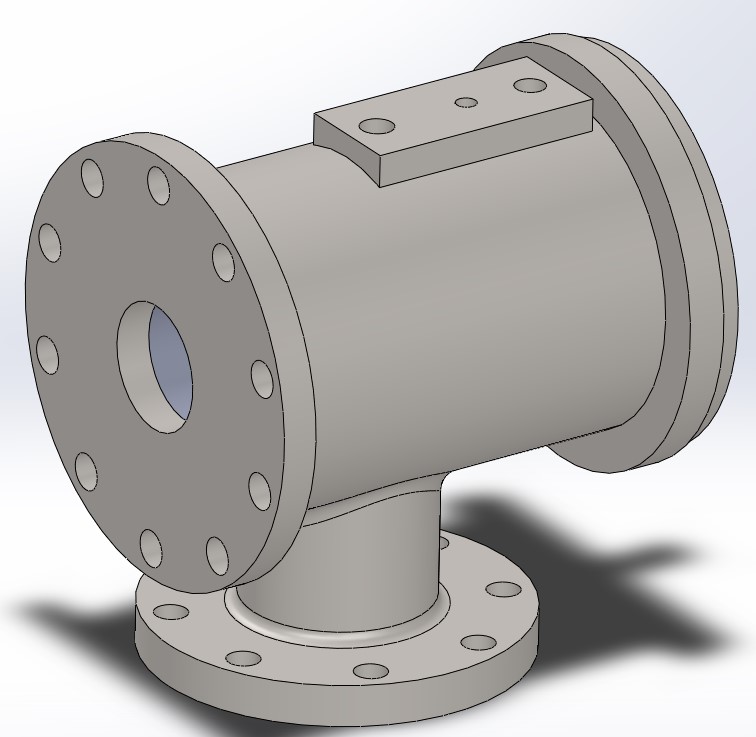
- Case Study: The recent Apollo 11 documentary highlighted that the rocket suffered a ‘hydrogen valve leak in the hours before launch. Technicians were still trying to fix it even as the astronauts were boarding and were presumably successful in sorting, NASA’s star-crossed Space Launch System moon rocket was grounded for the second time in five days, this time by a large hydrogen leak in a fuel line quick-disconnect fitting in Artemis 1.
- Solutions: we developed a compact AI Leakless Feed/drain valve, and a similarly designed quick disconnect, the valve has a plug one action chamber to open the valve by ground commands, and one action chamber for an abroad red crew to provide a dea seal against the seat in case leak, the plug is designed with two critical features: a position seal to prevent FOD with triple seals, a moving stabilizer to prevent the plug from jamming without causing vibrations, AI high-level mode and low-level control mode, the High-level control include (1) open by ground commands, abroad red crew command to prevent leaks, the low-level control includes self seating, the valve size is from 3″ to 12″, they are direct acting, light weights with various materials selections, pressure up to 22 bar, the medium includes lox oxygen, liquid fuels.
AI Propellant, Pogo-free throttling valve
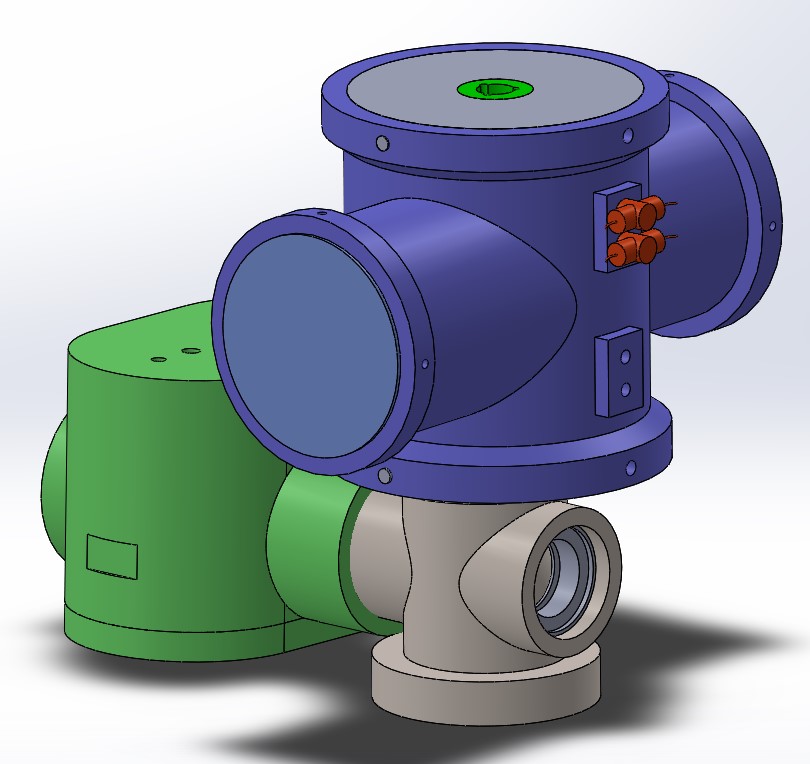
- Case Study: Almost 95 % of rocket explorations are caused by unplanned propellant feeding or leaks, most engines have a main valve to check the fluid feeding or a throttling valve to regulate the propellants. Since the propellants are liquid and incompressible fluid, any throttling only increases or decreases the fluid pressure, not the flow rate, the pogo is mainly caused by the throttling valves. So the additional operation is needed to release overpressure propellants, they are very complicated and slow, in case of emergence, and the shutdown operation takes time to release the propellants from the prevalve, turbo pump to the main valve, some efforts were made to close the prevalve, to shut down the turbo pump, but they fail because of the water hammer which can damage the system or just too late to save the rockets.
- Solutions: Why so far, there are no good solutions because throttling propellents is very complicated, even some design calculations can be used to decide the lox and fuel ratio, but in reality, the ratios are various, moreover, a feeding rate at the start is different from the full rate of pump output, even the valve is fully open, it doe not means that full flow rate is reached, on the other hand, the pressure or temperature in the nozzle can be too high, the ratio or the flow rate should be changed. So we developed an AI Popllentat throttling valve with High-level control of solenoid valves, flow rate sensors, to start or shut down the valve, and low-level control to throttle the valve for the flow rate between a designed rate and full rate with self-feedback and self-acting. Size from 3″ to 12″, pressure up to 6000 psi.
Shaftless. cavitation free, Inducerless Turbo Pump
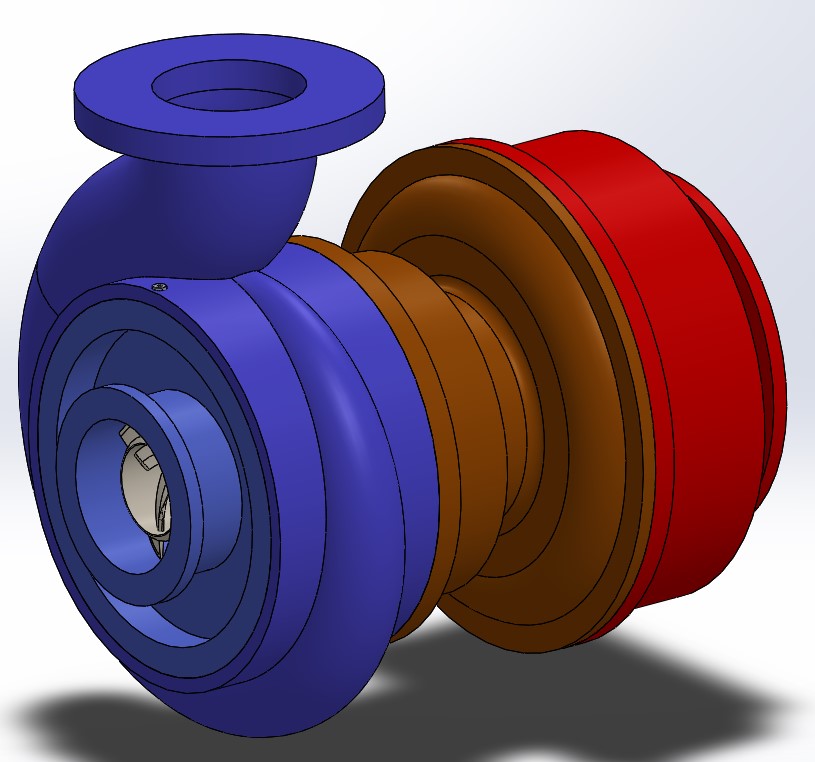
- Case Study: All current turbo pumps have an inductor with centrifugal blades, some systems with low-pressure and high-pressure pumps, and a ridged shaft with flexible bearings, a standard rotor dynamics design. What is wrong, here are the reasons, those features cause the pump to vibrate, and the speed limit of the shaft rotation, increase the ratio between dry volume and wet volume, and waste a great amount of input energy into the low efficient part of the pump, and more high side of the pump impeller and the circulation of fluids between the blades, since the input energy from the shaft can be destroyed or created, the unconverted energy can damage the impeller and casing, bearings and increase the temperature of propellents.
- Solutions: The turbopump is the heart of the liquid rocket engine, we studied all turbo pumps around the world to develop the first shaftless and inducer less, turbo pump to overcome the challenges of the pumps, here are those features (1) A rotor is designed to replace the shaft to reduce the weight and insolate the heat from turbine wheel and to increase the fluid passage areas (2) The design of rotodynamic is based on ridge bearing with a flexible rotor, so the clearance of the bearing can be minimized, the rotor speed can reach the highest level, no other pump can reach (3) a balanced pump wheels design to cancel side load on the impeller to reduce sideload on bearings and minimize fluid circulations between blades and increase numbers of blades in high power zone to increase the efficiency of energy conversion between the rotor and output fluid by 38 % (4) the bearings are designed to increase contract traces to 3 to eventually distribute the load, so the life of the bearing can increase by 30 % more, a simple signature sound can bed use to inspect the bearings with disassembly.
Leakless, FOD Proof, jamming-less solenoid valve
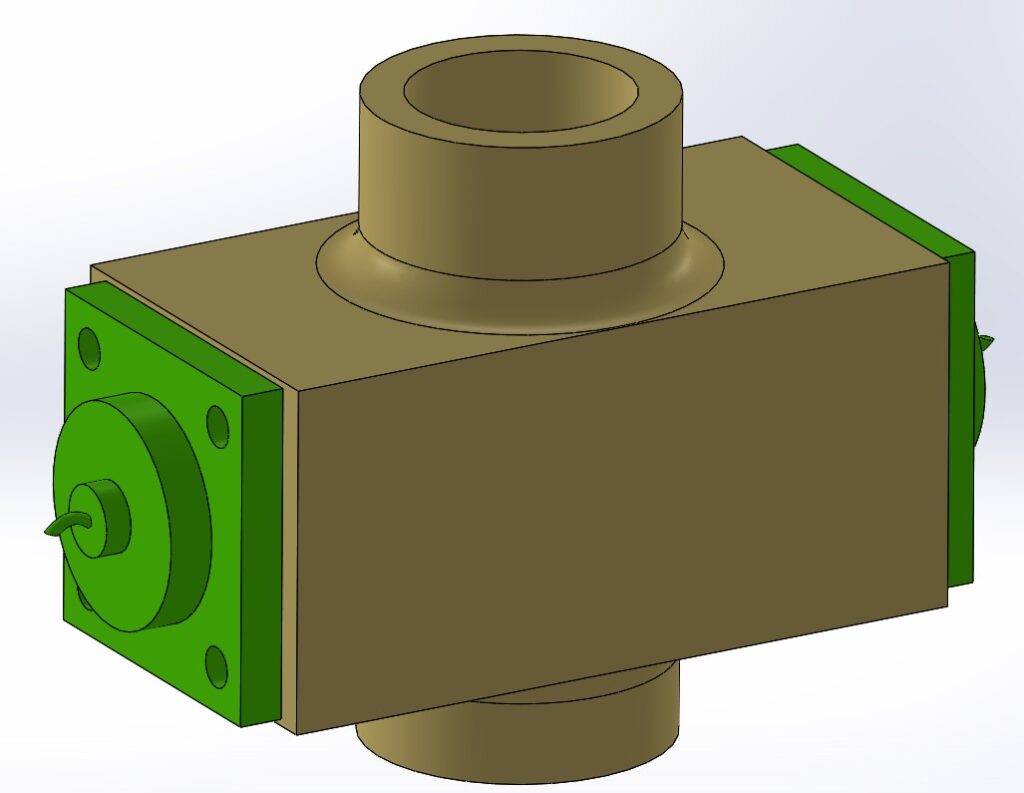
- Case Study: (1) All solenoid valves in rockets are not fully redundant, the best ones have redundant coils, but do not meet the NASA, single fault tolerance standard (2) FOD, is a major issue for poppet for solenoid valve failures, during the August 2021 launch window some issues were detected with 13 propulsion-system valves in the spacecraft before launch. a joint NASA––Boeing team spent weeks trying to understand what caused the thrusters to malfunction, in the end, the ground team was able to replicate the thrust degradation and tied it back to a Teflon seal that had been deformed by a buildup of heat. and another issue (3) high spring force and high solenoid force can increase the action failure rate (4) the directing valve is up to 3/8″ to 1/2 to 1″ are two staged solenoid valves, they become very complicated and subject to many failures.
- Solutions: we developed a compact solenoid valve with two independent coils, two independent poppets, two independent seats, and two small springs to overcome frications, the poppet is designed with two critical features: a position seal to prevent FOD with triple seals, a moving stabler to prevent the poppet from jamming without causing vibrations, the valve size is from 1/4″ to 1″, they are direct acting, light weights with various materials selections, pressure up to 6000 psi, the medium include helium, nitrogen, and other gases.
Springless, chatter-less, leakless redundant relief valve
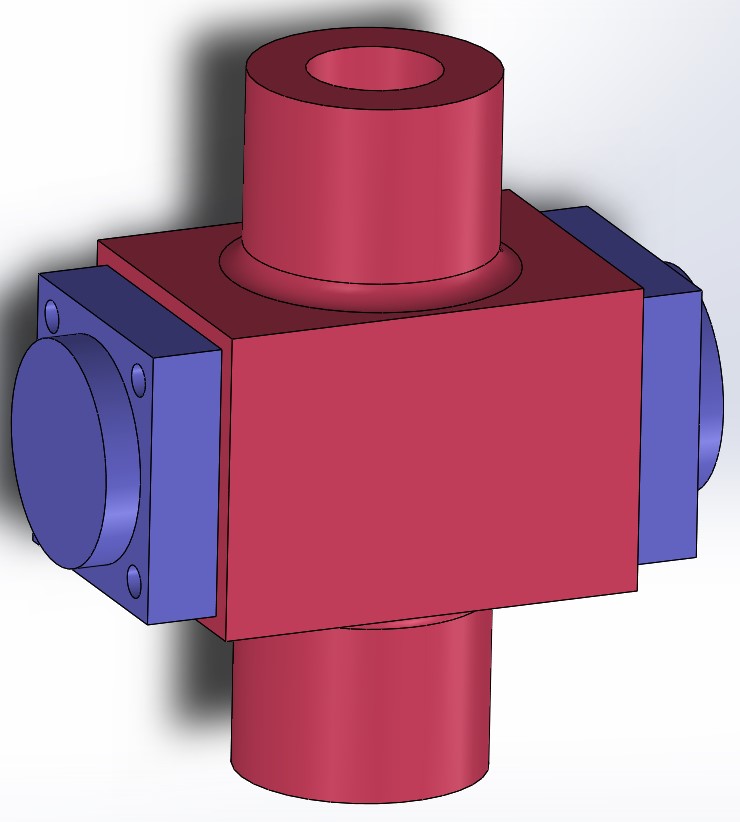
- Case Study: (1) All relief valves in rockets are not fully redundant, or most two relief valves are arranged in series, but this application is wrong, because the relief valve is designed to control inlet pressures, and the second relief valve is used to control the outlet pressure, so they do not meet the NASA, single fault tolerance standard (2) the constant poppet chats are due to nature of design that is based on liquid or other industry standards and cause poppet is seized with the seat (3) ut ones are redundant coils are redundant and (4) FOD is a major issue for poppet for the valve failures (5) high spring force, so they are weighted (5) the directing valve is up to 3/8″ to 1/2 to1 ” are two staged solenoid valve, they are very complicated and subject to many failures.
- Solutions“: We developed a redundant pressure regulator with two poppets, two seats, and two two-stage gas expansion mechanisms, with two-stage gas expansion mechanisms, the expanded or regulated gas becomes irrecoverable, and eliminates the chatters, and the second-stage expansion chamber is used to sense the outlet pressure and to regulate the inlet pressure, the poppet has two critical features, a position seal against the seat, and a moving stabilizer to prevent the poppet from jamming and moving vibration, Size 1/4″ to 1”, pressure range from 6000 psi to 100psi, the medium includes all gases in the rockets.
Springless, chatter-less, leakless check valve
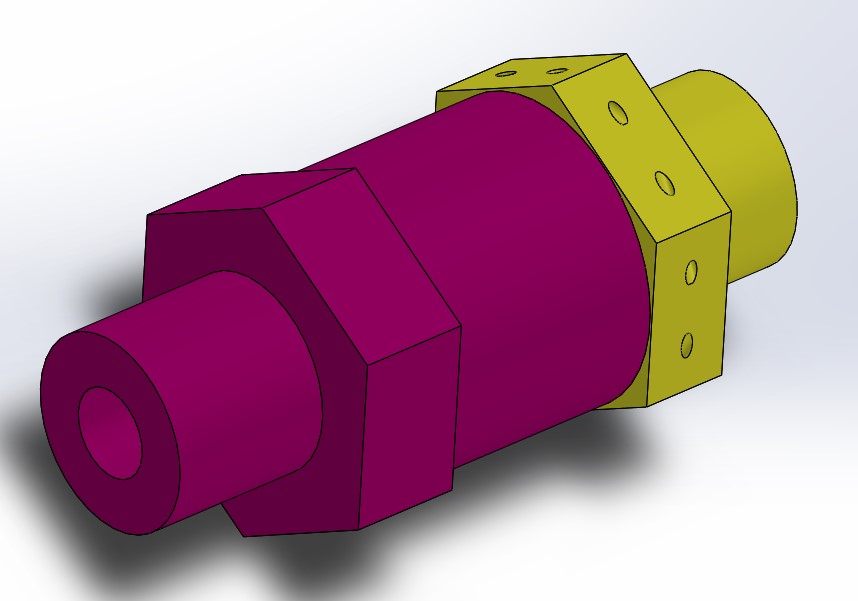
- Case Study: (1) All check valves in rockets are biased with spring, which causes poppet chatter and seized with the seat (2) the constant poppet chats are due to the nature of design that is based on liquid or other industry standards and cause poppet is seized with the seat (3) the small check valves have screwed in joint method and wired locked, which is expensive and time-consuming (4) the poppet movement with the spring is unstable and cause poppet jamming (5) FOD is a major issue for poppet for the valve failures.
- Solutions: We developed a springless check, the poppet has two critical features, a position seal against the seat, a moving stabilizer to prevent the poppet from jamming and moving vibrations, and a simple axal secure the screw joint, the poppet has two critical features a position seal the seat, and a moving stabilizer to prevent the poppet from jamming and moving vibration, Size 1/4″ to 1″, pressure range from 6000 psi to 100psi, the medium includes all fluids in the rockets.
Spring-less, Chatter-less Gas Pressure Regulator
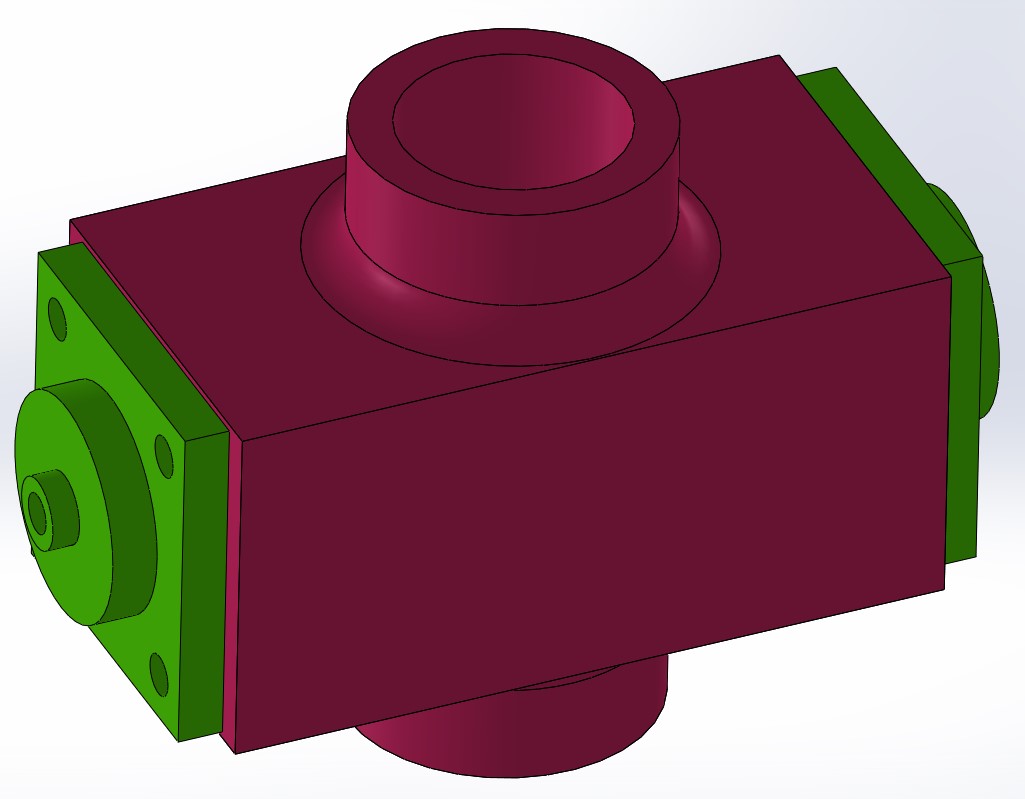
- Case Study (1) All pressure regulators in rockets are not fully redundant, in some cases, two regulators are arranged in series, but this application is wrong, because the pressure regulator is designed to control outlet pressures, so the second regulator is used with a regulated inlet pressure control of the first regulator, they do not meet the NASA, single fault tolerance standard and (2) the pressure regulator is designed based on liquid (incompressible fluid ) and causes chatter and unstable regulated pressure, the constant chatters cause the poppet to be seized with the seat (3) FOD is a major issue for the poppet for the regulator failures (4) vibrations, due to the spring forces and nature of the poppet movements between open and closed positions, the failed Peregrine moon lander on January 8, 2024, is a case in point, where the pressure control valve PCV2 has a fatal design, a moving plunge with o ring secured by threads, no redundancy.
- Solutions: We developed a redundant pressure regulator with two poppets, two seats, and two two-stage gas expansion mechanisms, with two-stage gas expansion mechanisms, the expanded or regulated gas becomes irrecoverable, and eliminates the chatters, and the second-stage expansion chamber is used to sense the outlet pressure and to regulate the inlet pressure, the poppet has two critical features, a position seal against the seat, and a moving stabilizer to prevent the poppet from jamming and moving vibration, Size 1/4″ to 1″, pressure range from 6000 psi to 100psi, the medium includes all gases in the rockets.
Rocket engine parts are subject to the International Traffic in Arms Regulations (ITAR), and may not be exported, released, or disclosed to non-U.S. Citizens inside or outside the United States without prior written approval from the U.S. Department of State.
Renewable energy
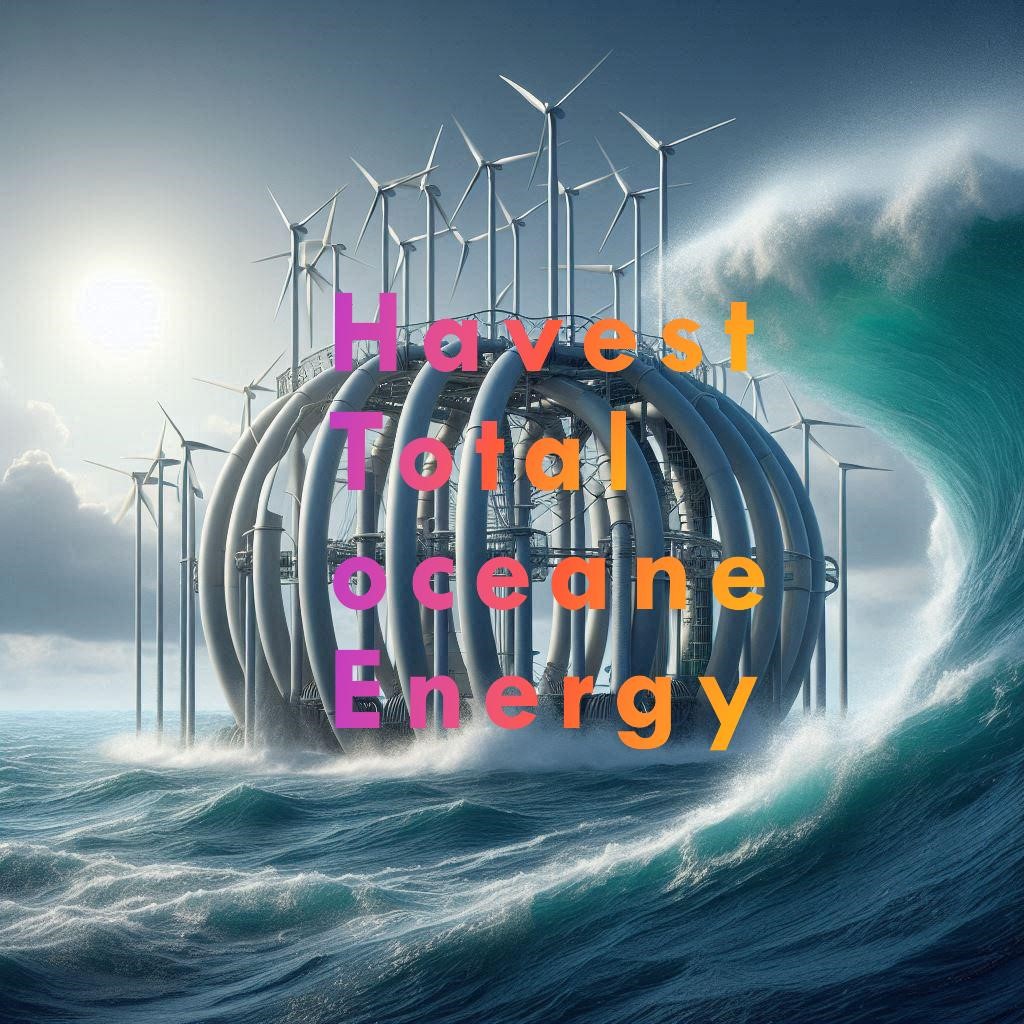
This ultimate renewable energy machine,( US Patent 11441540, 11428211 ) is an an all-depth offshore turbine system with a disruptive methodology and innovative technology, which changed 150 histories of the turbines. The true turbine system is a volume-based power system ( Kw/ M^3 ) instead of the current area-based power system ( Kw/M^2) decentralized power systems to provide power where customers are located and greatly reduce transportation and transmission costs unlike the fossil power system or gigantic wind turbine farms and has a top wind turbine subsystem, a middle wave turbine subsystem with solar panels and a bottom tidal turbine subsystem with efficiency beyond Betz limit of 59%, the turbine system includes a breakthrough turbo-technology with robust shaft-less twin rotors and dual-power zone blade structure to harness all ocean energy in a synergic manner or individually, this system has all-season safety features for birds, marine life, humans, and itself, is modularized and scalable for low LCOE < $0.10 kWh and provides reliable electricity 24/7, If the steam engine brought us the Industrial Revolution, then this quintessentially American secret weapon would bring the USA to the top of the world for the 21st-century energy revolution and be the ultimate fossil energy alternative.
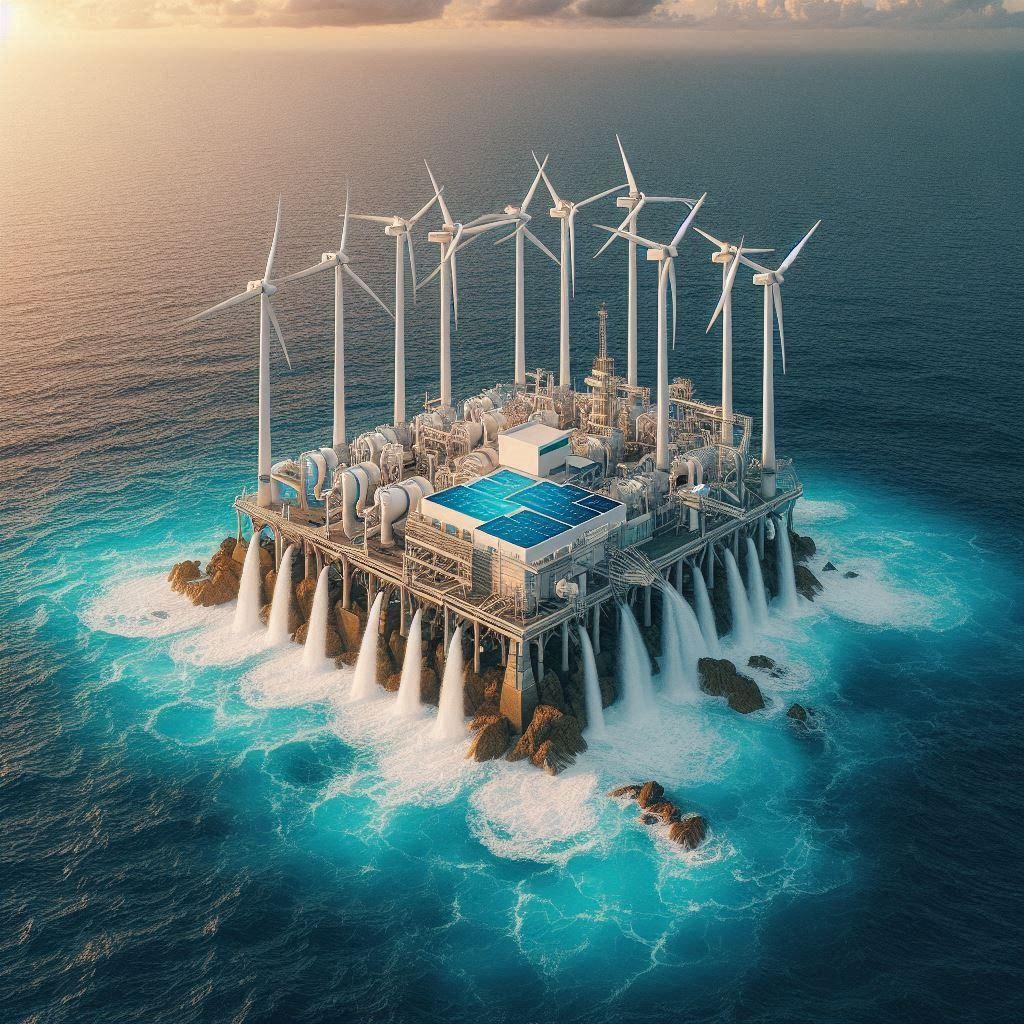
100 % Renewablely Powered Desalination Stations
a 100% renewably-powered desalination/water purification station (US Patent No US 11685679B2) for universal applications. The station is disruptive, scalable, amphibious, and deportable to seawater, brackish, or spill oil sites for simple wave-powered and autonomous operations. The station has a mooring assembly with pumping-purification-delivery subsystems powered by wave and solar energies. The pumping sub-systems have the simplest, most efficient wave push/pull pump mechanisms powered by amplified wave centrifugal forces. The mechanical purifications have turbine filters; reverse-osmosis filters, forward-osmosis filters, and relief valves to backwash buildups or release water by collecting spill oil. The solar thermal purifiedions are provided with distilling processes under vacuum conditions. The delivery subsystems with wave turbines and solar panels generate electricity, propelling and transferring the stations for delivering fresh waters to destinations under GPS guide with the lowest LCOW.
.